How to Choose the Best Horizontal Corrugated Roofing Tile for Your Home
By:Admin
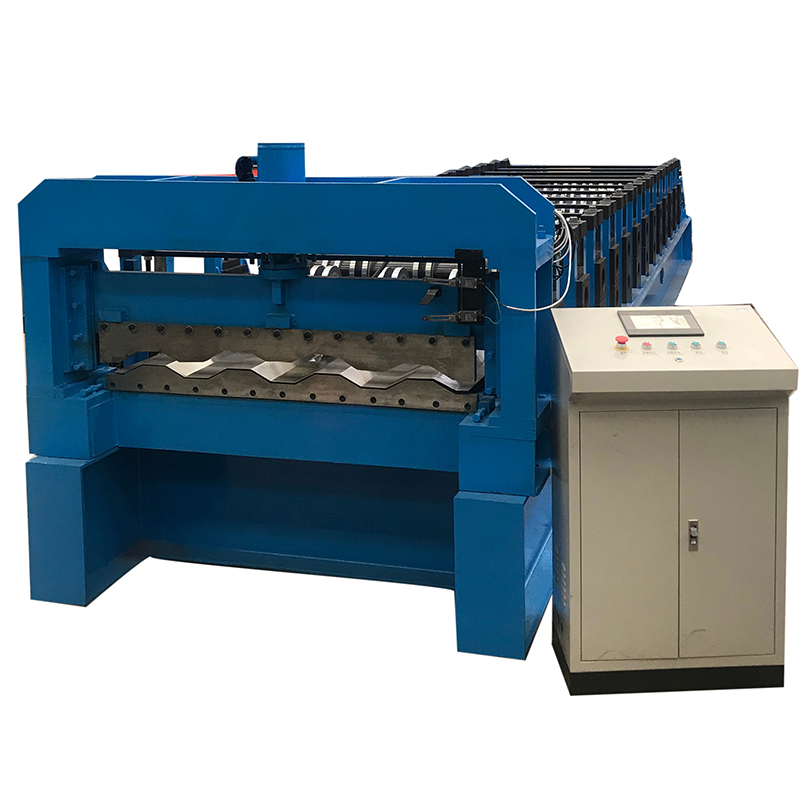
Horizontal Corrugated Roof Tile: A Revolutionary Addition to the Roofing Industry
[Introduction]
In recent times, the roofing industry has witnessed a remarkable invention that is set to transform the way we approach roofing solutions. Horizontal Corrugated Roof Tile, an innovative product brought to you by a leading manufacturer in the industry, is here to revolutionize the roofing landscape. With its unique features and superior quality, this new addition offers numerous advantages over traditional roofing options. Let us delve deeper into the world of Horizontal Corrugated Roof Tiles and explore how they are paving the way for a brighter and more sustainable future.
[Body]
1. The Concept behind Horizontal Corrugated Roof Tile:
Horizontal Corrugated Roof Tile is the result of years of research and development by a dedicated team of experts in the field. This roofing solution aims to provide a durable, aesthetically pleasing, and environmentally friendly alternative to conventional roofing options. The concept behind this innovative product stems from the need to address the limitations of traditional roofing materials and to provide a superior solution that caters to the evolving demands of the industry.
2. Unparalleled Durability:
One of the key features of Horizontal Corrugated Roof Tile is its unmatched durability. Made from high-quality materials, these tiles can withstand extreme weather conditions, including strong winds, heavy rain, and even hailstorms. Unlike traditional roofing options that often suffer from structural damage and require frequent repairs, Horizontal Corrugated Roof Tiles have been engineered to last for decades, reducing maintenance costs significantly.
3. Aesthetics and Design:
Not only does Horizontal Corrugated Roof Tile provide exceptional durability, but it also offers a wide range of design options to suit different architectural styles. The sleek and modern design of these tiles adds a touch of sophistication to any building, making it an ideal choice for both residential and commercial projects. With a variety of color options available, customers can select the perfect shade to complement their overall building design.
4. Environmental Benefits:
In today's world, sustainability plays a pivotal role in decision-making when it comes to construction materials. Horizontal Corrugated Roof Tile aligns perfectly with this mindset, as it is made from recycled and recyclable materials. By opting for this eco-friendly roofing solution, customers can contribute to reducing their carbon footprint, while also enjoying the numerous benefits it offers.
5. Easy Installation and Cost-Effectiveness:
Horizontal Corrugated Roof Tile not only saves time but also money during the installation process. Thanks to its lightweight design, these tiles are easier to handle and require less labor compared to traditional materials. This results in reduced installation costs and quicker project completion times. Moreover, the long lifespan of these tiles means that customers can enjoy significant long-term savings by minimizing the need for frequent repairs or replacements.
6. Testimonials and Success Stories:
Since its introduction to the market, Horizontal Corrugated Roof Tile has received high praise from contractors, architects, and customers alike. Numerous success stories have emerged, showcasing the transformation of buildings and the immense satisfaction of customers who have opted for this innovative roofing solution. Whether it's residential complexes, commercial buildings, or industrial structures, the versatility of Horizontal Corrugated Roof Tile shines through in all applications.
[Conclusion]
In conclusion, Horizontal Corrugated Roof Tile represents a significant advancement in the roofing industry. With its durability, sustainability, and aesthetic design, this revolutionary product is redefining the standards for roofing solutions. The innovative concept, combined with the company's commitment to quality and customer satisfaction, ensures that customers receive a superior product that surpasses their expectations. As the roofing industry continues to evolve, Horizontal Corrugated Roof Tile stands tall as a testament to the ingenuity and potential for positive change within the field.
Company News & Blog
Innovative Profiling Equipment for Creating Glazed Tiles
Title: Advanced Profiling Equipment Revolutionizes Glazed Tile ManufacturingIntroduction:In a groundbreaking development that is set to transform the glazed tile manufacturing industry, a leading company has unveiled its latest innovation - advanced profiling equipment. This cutting-edge technology eliminates the need for manual profiling, streamlining the production process and ensuring unparalleled precision and efficiency. By leveraging this state-of-the-art machinery, manufacturers can now produce an exquisite range of glazed tiles in a faster, more cost-effective, and sustainable manner.Innovative Technology:The newly-introduced advanced profiling equipment is the result of extensive research and development by a renowned manufacturer. By fusing automation and computer-controlled precision machinery, this equipment allows for the shaping and profiling of glazed tiles in a highly accurate and efficient manner. With superior profiling capabilities, the equipment can achieve intricate designs and impeccable finishing, rendering each glazed tile a work of art.Enhanced Precision:The traditional method of manual profiling often resulted in inconsistencies in tile shape, leading to production delays and significant material wastage. However, with the advent of advanced profiling equipment, such concerns are now a thing of the past. The computerized controls and precise movements of the machinery ensure that each tile is uniform, with perfectly calibrated dimensions as specified by the manufacturer. This increased precision results in a seamless construction process and facilitates easy installation for end-users.Streamlined Production and Increased Efficiency:One of the primary advantages of the new profiling equipment is its ability to significantly boost production capacity while minimizing manufacturing time. The advanced technology automates various stages of the profiling process, including cutting and shaping, thereby reducing the reliance on manual labor. This not only speeds up the production cycle but also reduces costs associated with human errors and worker fatigue. Additionally, the machinery's efficiency ensures a higher output of glazed tiles, meeting market demands effectively.Sustainable Manufacturing:As the global focus on sustainable practices intensifies, the need for eco-friendly manufacturing processes has become more critical than ever. Advanced profiling equipment is a solution to this challenge. By minimizing resource wastage and optimizing the production process, this machinery dramatically reduces the carbon footprint of glazed tile manufacturing. Moreover, it promotes the use of recyclable materials, contributing to the overall sustainability of the industry.Durability and Longevity:The integration of advanced profiling equipment ensures that glazed tiles produced possess exceptional durability and longevity. The precision cutting and shaping techniques employed by the machinery create tiles that fit seamlessly and interlock securely. This eliminates the risks of cracks, breakages, or uneven installation, guaranteeing a reliable, long-lasting flooring or walling solution for customers across various sectors.Revolutionizing Tile Design:The advent of advanced profiling equipment has unlocked a new era of design possibilities for glazed tiles. Manufacturers can now experiment with intricate shapes, beveled edges, and unique aesthetics that were previously difficult to achieve through manual profiling. This has led to an explosion of creativity and innovation in the industry, with customers benefiting from an extensive range of designs and patterns to suit their individual preferences and requirements.Conclusion:The introduction of advanced profiling equipment marks a significant turning point in the glazed tile manufacturing industry. This cutting-edge machinery not only streamlines production processes but also ensures unparalleled precision, efficiency, sustainability, and durability. With limitless design possibilities, the application of this advanced technology promises to revolutionize the realm of glazed tiles, enhancing the quality of construction projects worldwide.
Advanced Sheet Forming Equipment for Horizontal Profiles Unveiled - Exciting Opportunities Await!
**Title: Innovative Horizontal Profiled Sheet Forming Equipment Revolutionizes Manufacturing Industry**Introduction:In recent years, the manufacturing industry has experienced significant advancements in technology and automation, enabling businesses to enhance their production processes and stay ahead in the competitive market. One such groundbreaking innovation is the Horizontal Profiled Sheet Forming Equipment, transforming the way companies manufacture sheet metal products. This cutting-edge technology, developed by a renowned industry leader, promises to revolutionize the manufacturing process, offering increased efficiency, precision, and versatility.Company Introduction:Founded in [year], [Company Name] has established itself as an industry-leading manufacturer, specializing in developing state-of-the-art machinery and equipment for metal fabrication. With a commitment to innovation and a relentless pursuit of excellence, the company has consistently pushed boundaries, delivering groundbreaking solutions to meet the ever-evolving needs of their customers. [Company Name] combines top-notch engineering expertise, advanced technology, and a customer-centric approach to deliver products that exceed expectations.Revolutionizing Manufacturing with Horizontal Profiled Sheet Forming Equipment:The Horizontal Profiled Sheet Forming Equipment, developed by [Company Name], is set to revolutionize the manufacturing industry. This cutting-edge system offers an efficient, precise, and reliable solution for companies involved in sheet metal fabrication. With its unique design and advanced features, the equipment provides several key advantages over traditional forming techniques.1. Improved Efficiency:The Horizontal Profiled Sheet Forming Equipment streamlines the manufacturing process, significantly improving efficiency and reducing production time. It incorporates automated controls and advanced software algorithms, eliminating manual labor and maximizing productivity. The equipment's high-speed capabilities allow for faster throughput and quicker turnaround times, enabling companies to meet tight project deadlines while maintaining exceptional quality standards.2. Enhanced Precision:Precision is of utmost importance in the manufacturing industry, and the Horizontal Profiled Sheet Forming Equipment delivers unrivaled accuracy. Its advanced sensors and measurement systems ensure precise control of various parameters during the forming process, resulting in consistently high-quality products. The equipment's innovative tooling system enables intricate profiling, embossing, and shaping of metal sheets with micron-level precision, opening up new possibilities for complex design implementations.3. Versatility and Customization:Flexibility is a key requirement in today's market, where customization and adaptability play crucial roles. The Horizontal Profiled Sheet Forming Equipment offers an unparalleled level of versatility, allowing manufacturers to produce a wide range of sheet metal products. From architectural profiles and roofing elements to automotive components and aerospace parts, the equipment's modular design facilitates quick changeovers and adjustments, ensuring seamless transitions between different product lines.4. Cost-effective and Sustainable:In addition to its operational advantages, the Horizontal Profiled Sheet Forming Equipment helps businesses achieve cost savings and reduce environmental impact. Its energy-efficient design, coupled with optimal material utilization, minimizes waste and energy consumption, translating into significant cost reductions and a smaller carbon footprint. By embracing this innovative technology, manufacturers can align their processes with sustainable manufacturing practices while simultaneously improving their bottom line.Conclusion:With its groundbreaking features and numerous benefits, the Horizontal Profiled Sheet Forming Equipment created by [Company Name] is poised to revolutionize the manufacturing industry. Through increased efficiency, enhanced precision, and unmatched versatility, this cutting-edge technology offers manufacturers a competitive edge in a rapidly evolving market. As companies strive for greater productivity, superior quality, and sustainable operations, the Horizontal Profiled Sheet Forming Equipment presents a game-changing solution, transforming the way sheet metal products are manufactured.
Pros and Cons of All-In-One vs. Multiple Single Layer Roll Forming Machines: A Comprehensive Comparison
, Multiple Roll Forming Machines, All-in-one Roll Forming Machine, Double layer Roll Forming Machine, Roll Forming Machinery.When it comes to roll forming, there are a few different options to consider. One decision that needs to be made is whether to choose an all-in-one roll forming machine or multiple single layer roll forming machines. Both options have their pros and cons, so it ultimately depends on the specific needs and preferences of the user.Single layer roll forming machines are a popular choice for many manufacturers. These machines are designed to create a continuous sheet of metal by bending it into a certain shape. One of the advantages of using a single layer roll forming machine is the ability to produce a high volume of products quickly and efficiently. Since the machine only focuses on one layer at a time, it's easier to control the quality of each product and ensure that each one is consistent.Another advantage of using a single layer roll forming machine is the ability to customize the process based on the specific needs and materials being used. These machines are often designed to be highly flexible, allowing for adjustments to be made based on the thickness and type of material being used.However, one of the downsides of using a single layer roll forming machine is the need for multiple machines if a manufacturer needs to produce multiple layers. This can be a disadvantage if a manufacturer is trying to minimize the number of machines being used in their production process.On the other hand, all-in-one roll forming machines are designed to be highly versatile and efficient. These machines are capable of producing multiple layers of metal at once, which can help streamline the production process. Additionally, all-in-one roll forming machines are often designed to be highly automated, which can help reduce the need for labor and increase overall efficiency.One of the disadvantages of using an all-in-one roll forming machine is the potential for decreased quality control. Since these machines are designed to focus on multiple layers at once, it can be more difficult to ensure that each product is consistent and meets the desired quality standards.Another potential disadvantage of using an all-in-one roll forming machine is the cost. These machines are typically more expensive than single layer roll forming machines, which can be a disadvantage for smaller manufacturers or those with limited budgets.Finally, double layer roll forming machines are another option to consider. These machines are designed to produce two layers of metal at once, which can help increase production efficiency and reduce the need for multiple machines. However, like all-in-one roll forming machines, double layer roll forming machines can be more expensive and may have lower quality control.Ultimately, the decision to choose between an all-in-one roll forming machine and multiple single layer roll forming machines will depend on a variety of factors, including the specific needs and preferences of the manufacturer. Both options have their advantages and disadvantages, so manufacturers should carefully consider their options before making a final decision.
High-Quality Sheet Metal Punching Machine with 22KW Power – C Frame Casting Fuselage J23 Series
Title: Leading Manufacturer Introduces High-Quality Sheet Metal Punching Machine for Enhanced Efficiency Introduction:With the rising demand for precision and efficiency in the metalworking industry, {Company Name}, a prominent player in the manufacturing sector, has unveiled its latest innovation, the 22KW Power Steel Hole Punching Machine C Frame Casting Fuselage J23 Series. This cutting-edge machine promises to revolutionize the sheet metal punching process, providing unparalleled quality and performance for diverse industrial applications.Innovative Features and Superior Quality:The 22KW Power Steel Hole Punching Machine demonstrates the company's unwavering commitment to delivering outstanding products. This state-of-the-art machine incorporates a robust C Frame Casting Fuselage, enhancing its stability and durability. The use of high-quality materials ensures that it can withstand the rigorous demands of heavy-duty industrial operations.The machine boasts an impressive 22KW power capacity, allowing it to effortlessly handle various sheet metal materials. Whether it is stainless steel, aluminum, or mild steel, this punching machine guarantees a smooth and precise punching process, resulting in impeccable finished products.Uncompromising Precision and Efficiency:The J23 Series Sheet Metal Punching Machine is designed to deliver exceptional precision and efficiency. Equipped with advanced technology, the machine ensures accurate hole punching and seamless integration with other fabrication processes. Its cutting-edge control system allows operators to program and execute complex punching patterns effortlessly, reducing human error and enhancing overall efficiency.Additionally, the J23 Series offers superior versatility, enabling manufacturers to produce a wide range of products without compromising quality. From intricate designs to high-volume production, this machine can meet the diverse needs of various industries, including automotive, electronics, and appliances.High-Performance Components and Enhanced Safety:{Company Name} understands the significance of incorporating safety features into their machines. The 22KW Power Steel Hole Punching Machine ensures the well-being of operators with comprehensive safety mechanisms. These include emergency stop buttons, overload protection, and protective guards to prevent accidents and injuries in the workplace.Furthermore, the company's commitment to sustainability and energy efficiency is evident in the machine's design. The J23 Series implements energy-saving technologies, optimizing power consumption during operation. This not only reduces the carbon footprint but also delivers cost savings for businesses, aligning with the global push for sustainable manufacturing practices.Commitment to Customer Satisfaction and Service:{Company Name} prides itself on its dedication to customer satisfaction. With the introduction of the 22KW Power Steel Hole Punching Machine, the company aims to meet and exceed the expectations of clients worldwide. {Company Name}'s team of highly skilled technicians and engineers are readily available to provide training, installation support, and routine maintenance for seamless machine operation.Conclusion:The introduction of the 22KW Power Steel Hole Punching Machine C Frame Casting Fuselage J23 Series solidifies {Company Name}'s position as a leading manufacturer in the industry. With its superior quality, precise performance, enhanced efficiency, and commitment to customer satisfaction, this machine is set to revolutionize the sheet metal punching process, empowering manufacturers to achieve exceptional results.
Revolutionizing Manufacturing: Discover the Advanced Metal Panel Production Machine
Profiled Metal Panel Manufacturing Machine Revolutionizes the IndustryIn a groundbreaking development for the metal panel manufacturing industry, a highly reputable company has unveiled its innovative profiled metal panel manufacturing machine. This cutting-edge technology is set to revolutionize the production process, enhance efficiency, and deliver high-quality metal panels like never before.With a commitment to advancing manufacturing capabilities, this state-of-the-art machine is designed to achieve precision and consistency in profiled metal panel production. The company's dedication to research and development has resulted in a game-changing solution that addresses the evolving needs of the industry, while also meeting strict quality standards.The profiled metal panel manufacturing machine boasts an array of advanced features that significantly streamline the production process. The machine's automated functionalities reduce human error, ensuring exceptional product quality and productivity. With minimal manual intervention required, manufacturers can enjoy increased efficiency, saving time and costs in the long run.This revolutionary machine's versatility is another noteworthy aspect that sets it apart from its competitors. It is equipped to process various types of materials, including steel, aluminum, and even composite panels. This adaptability showcases the company's commitment to cater to a wide range of applications and industry requirements.The machine's cutting-edge technology enables manufacturers to produce a variety of profiled metal panels, such as corrugated sheets, standing seam panels, and insulated panels. This diversification in product offerings allows companies to expand their portfolios, cater to different client preferences, and tap into new markets.Furthermore, the machine's precise control system ensures accuracy in panel dimensions, angles, and shapes. Manufacturers can confidently produce panels with intricate designs and complex profiles, meeting the unique specifications of individual projects. This level of precision and customization is highly sought after in industries such as architecture, construction, and automotive manufacturing.Equally important is the machine's emphasis on sustainability and eco-friendliness. With the growing global concern for environmental impact, the company has integrated energy-efficient technologies into the manufacturing process. This not only reduces carbon emissions but also lowers operating costs for manufacturers, contributing to a greener and more sustainable future for the industry.The introduction of this profiled metal panel manufacturing machine signifies the company's commitment to staying at the forefront of technological advancements. By constantly pushing the boundaries of innovation, they ensure that their clients have access to cutting-edge machinery that provides a competitive edge in the marketplace.Additionally, the company's dedication to customer satisfaction is evident in its comprehensive technical support and after-sales services. They offer professional training programs to ensure manufacturers can fully leverage the machine's capabilities, maximizing productivity and profitability. Furthermore, a dedicated customer service network ensures quick response times and assistance whenever needed.Industry professionals have expressed great anticipation for this game-changing machine's impact on the metal panel manufacturing sector. With its advanced features, adaptability, precision, and focus on sustainability, the machine addresses the evolving needs of the industry while optimizing production processes for enhanced efficiency.The profiled metal panel manufacturing machine is set to revolutionize the industry, empowering manufacturers to deliver high-quality panels efficiently and sustainably. It represents a significant milestone in the metal panel manufacturing sector and reinforces the company's commitment to innovation, customer satisfaction, and industry leadership. With this groundbreaking technology, a new era has dawned upon the metal panel manufacturing industry.
How to Choose a Standing Seam Roof Panel Machine for Your Business
Title: Advanced Standing Seam Roof Panel Machine Revolutionizing Roofing IndustryIntroduction:With the constant need for efficient and innovative solutions in the roofing industry, the introduction of an advanced Standing Seam Roof Panel Machine (name omitted) is set to revolutionize the way roofs are manufactured and installed. Developed by a reputable company known for their dedication to quality and precision engineering, this state-of-the-art machine promises to streamline the roofing process while offering enhanced durability and sustainability. Let's delve into the features and benefits of this cutting-edge technology.1. Efficiency and Precision:The Standing Seam Roof Panel Machine combines years of experience with advanced engineering to deliver a machine that is highly efficient and accurate in its operations. The machine is equipped with an automated control system, allowing for precise and consistent panel measurements, ensuring a perfect fit with minimal waste. With the ability to produce up to 60 feet of roof panel per minute, this innovative technology significantly reduces production time, increasing overall efficiency and productivity.2. Durability and Sustainability:In line with the company's commitment to environmentally friendly practices, the Standing Seam Roof Panel Machine employs sustainable materials and construction methods to produce highly durable roofing panels. The machine's design incorporates high-strength steel and state-of-the-art coatings to ensure resistance against harsh weather conditions, corrosion, and UV radiation. These panels offer exceptional longevity, reducing the need for frequent repairs or replacements, ultimately resulting in cost savings for both homeowners and commercial builders.3. Versatility and Customization:One of the standout features of the Standing Seam Roof Panel Machine is its ability to produce a wide range of panel profiles, allowing for extensive customization options. Clients can choose from a variety of panel widths, seam heights, and surface finishes, catering to their specific architectural requirements and aesthetic preferences. This versatility enables architects and designers to create unique roofing designs that harmonize with the overall style of the structure. Additionally, the machine's versatility ensures compatibility with various installation methods, making it suitable for both residential and commercial applications.4. Safety and Ease of Use:The Standing Seam Roof Panel Machine prioritizes operator safety and ease of use. The machine is equipped with advanced safety features, including emergency stop buttons, safety light curtains, and interlocking systems, ensuring a high level of protection during operation. Additionally, it boasts a user-friendly interface, allowing operators to navigate through different settings and controls with ease. The machine's ergonomic design and intuitive controls enable seamless operation, reducing the risk of errors and accidents.5. Training and Technical Support:Recognizing the importance of proper training and continuous technical support, the company offers comprehensive training programs to ensure operators have the necessary skills to operate the Standing Seam Roof Panel Machine effectively. The training covers machine operation, maintenance, troubleshooting, and safety protocols. Additionally, the company provides ongoing technical support to address any queries or concerns raised by customers, further enhancing the overall user experience.Conclusion:The introduction of the Standing Seam Roof Panel Machine marks a significant leap forward in the roofing industry, revolutionizing the way roofs are manufactured and installed. Its exceptional efficiency, precision, versatility, and sustainability make it a game-changer for architects, builders, and homeowners alike. With an unwavering commitment to quality and customer satisfaction, the company behind this advanced technology continues to innovate, ensuring the continuous improvement and development of the roofing industry.
Top-Quality Metal Roll Forming Machine for Sale with Roof Panel Roll Forming Machine
Metal Roll Forming Machine for Sale: A Boon for the Construction IndustryThe construction industry is witnessing rapid growth and development, and with it, the demand for efficient and high-quality machinery. One such piece of equipment that has become indispensable in the construction sector is the metal roll forming machine. Known for its versatility, reliability, and precision, this machine has revolutionized the way metal panels and profiles are created. It offers a cost-effective solution for constructing roofs, walls, and other structural components.In line with the growing demand, Metal Roll Forming Machine, a renowned industry player, is now offering their top-of-the-line metal roll forming machines for sale.Metal roll forming machines are capable of shaping various metals, such as steel, aluminum, and galvanized iron, into customized profiles of different shapes and sizes. These machines utilize a continuous bending process, wherein the metal strip is fed through a series of rollers, gradually shaping it into the desired profile. The resulting products offer exceptional structural strength, durability, and aesthetics.Metal Roll Forming Machine offers a wide range of machines to cater to the diverse needs of the construction industry. Their roof panel roll forming machine is particularly sought-after due to its ability to efficiently produce high-quality roof panels. These panels not only enhance the visual appeal of buildings but also provide superior protection against adverse weather conditions.One of the key features that set Metal Roll Forming Machine apart is its commitment to quality. The machines they offer are manufactured using state-of-the-art technology, ensuring unrivaled precision and performance. These machines undergo rigorous testing and quality checks to meet international standards and provide customers with reliable and long-lasting solutions.Metal Roll Forming Machine prides itself on providing excellent customer service. Their team of experienced professionals assists clients in selecting the most suitable machine for their specific requirements. Offering comprehensive after-sales support, they ensure that customers receive training and technical assistance to maximize the utilization of the machines.Moreover, Metal Roll Forming Machine understands the importance of sustainability and the need to minimize the environmental impact of their operations. Their machines are designed to optimize energy efficiency while minimizing material waste during the roll forming process. By adopting eco-friendly practices, Metal Roll Forming Machine is leading the way towards a greener and more sustainable future in the construction industry.To further facilitate customer convenience, Metal Roll Forming Machine now offers their machines for sale online. The user-friendly interface of their website allows customers to browse through their product catalog, compare specifications, and make informed purchasing decisions. With just a few clicks, customers can now own a top-quality metal roll forming machine to meet their construction needs.In conclusion, the availability of metal roll forming machines for sale by Metal Roll Forming Machine comes as a boon for the construction industry. These machines provide an efficient and cost-effective solution for producing high-quality metal profiles and panels. With their commitment to quality, customer service, and sustainability, Metal Roll Forming Machine has established itself as a trusted and reliable provider of metal roll forming machines. By investing in their machines, construction companies can elevate their productivity, efficiency, and profitability, ultimately contributing to the growth and advancement of the construction sector.
Efficient Metal Siding Roll Forming Machine Unveiled in Latest News
Metal Siding Roll Forming Machine Revolutionizes the Construction IndustryThe construction industry is constantly evolving, searching for more efficient and cost-effective solutions to meet the demands of the ever-growing market. One such innovation making waves in the industry is the Metal Siding Roll Forming Machine. This machine, developed by an industry-leading manufacturer, is revolutionizing the way metal siding is produced and installed, offering significant benefits to both contractors and homeowners.The Metal Siding Roll Forming Machine is designed to automate the production process of metal siding, eliminating the need for tedious manual work. With its advanced technology and precise engineering, the machine is capable of producing high-quality metal siding panels quickly and efficiently. This not only saves time but also ensures accuracy and consistency in the final product.The machine operates by guiding a continuous strip of metal through a series of rollers and dies, gradually forming it into the desired shape. The metal strip is fed into the machine, and as it passes through each station, it undergoes various bending and shaping processes. The finished panels are then cut to the required length and can be easily collected for packaging or installation.One of the key advantages of the Metal Siding Roll Forming Machine is its versatility. It can produce a wide range of metal siding profiles, allowing contractors to cater to various architectural and design preferences. Whether it's traditional lap siding, vertical panels, or even custom profiles, the machine can accommodate different specifications. This versatility gives contractors the flexibility to meet the unique demands of each project.Additionally, the Metal Siding Roll Forming Machine offers significant cost savings compared to traditional manual methods. By automating the production process, manufacturers can reduce labor costs and minimize material wastage. The consistency and precision provided by the machine also eliminate the need for rework, further reducing expenses. These cost savings can trickle down to homeowners, making metal siding a more affordable and attractive option for them.Furthermore, the Metal Siding Roll Forming Machine can enhance the overall durability and performance of metal siding. The precise forming process ensures that the panels have consistent dimensions, minimizing the risk of gaps or misalignment during installation. This tight fit increases the siding's resistance to wind, moisture, and other environmental factors, making it a durable and long-lasting option for any building.The machine's efficiency and automation also reduce the manpower required for installation. Contractors can complete projects faster, as the panels are ready to be installed as soon as they are produced. This time-saving aspect not only improves project timelines but also reduces disruptions to homeowners and residents nearby.As an industry-leading manufacturer, [Company Name] has been at the forefront of developing and refining the Metal Siding Roll Forming Machine. With years of experience and expertise in the field, the company has continually improved the machine's design, ensuring optimal performance and reliability. Their commitment to innovation has made the Metal Siding Roll Forming Machine a game-changer in the construction industry.In conclusion, the Metal Siding Roll Forming Machine is revolutionizing the construction industry with its efficiency, versatility, and cost-effectiveness. By automating the production process, contractors can save time, reduce costs, and deliver high-quality metal siding panels. With its precise engineering and durability, the machine ensures that homeowners can enjoy a long-lasting and visually appealing product. Thanks to the innovative efforts of companies like [Company Name], the future of metal siding production and installation looks brighter than ever.
Advanced Machinery for Precise Coil Slitting and Rewinding
Coil Slitting and Rewinding Machine Brings Efficiency and Accuracy to Manufacturing ProcessesAs manufacturing processes become increasingly complex and demanding, companies are seeking innovative solutions to streamline their operations and improve their efficiency. One such solution is the Coil Slitting and Rewinding Machine, a cutting-edge piece of equipment that allows manufacturers to accurately and efficiently process large coils of material into smaller, more manageable rolls.The Coil Slitting and Rewinding Machine is ideal for a wide range of applications, from metalworking and plastics processing to paper and textile production. With its advanced technology and precision engineering, this machine can quickly and accurately cut and trim coils of material to the desired size and shape, ensuring consistent quality and performance.At {company name}, we are proud to offer a range of high-quality Coil Slitting and Rewinding Machines to meet the needs of our customers. Our machines are designed and manufactured to the highest standards, using only top-quality components and materials. We offer a variety of models to suit different needs and requirements, from compact, entry-level machines to high-speed, fully automated systems.One of the key advantages of our Coil Slitting and Rewinding Machines is their versatility. They can be used to process a wide range of materials, including steel, aluminum, copper, plastic, paper, and more, making them an ideal choice for a variety of industries and applications. Moreover, our machines can handle coils of different sizes and weights, from small rolls to large, heavy-duty coils.Another advantage of our Coil Slitting and Rewinding Machines is their precision and accuracy. Thanks to advanced sensors and computer-controlled systems, these machines can make precise cuts and trims, with tolerances as low as a few microns. This ensures that each roll is consistent in size and thickness, with no variation or defects.In addition to their precision and accuracy, our Coil Slitting and Rewinding Machines are also highly efficient and easy to use. They are designed to minimize waste and maximize productivity, with fast setup and changeover times, and intuitive controls that allow operators to quickly adjust settings and parameters.Overall, our Coil Slitting and Rewinding Machines are a valuable asset to any manufacturing operation, offering a range of benefits that can help improve efficiency, quality, and profitability. If you are interested in learning more about our machines and how they can benefit your business, please contact us today to schedule a consultation.
Cable Tray Pultrusion Machine: Advancements in FRP Technology Shake Up the Industry
Title: Cutting-Edge FRP Cable Tray Pultrusion Machine Revolutionizes the IndustryIntroduction:Pushing the boundaries of innovation, a leading company in the manufacturing sector has recently unveiled its latest breakthrough - an advanced FRP (Fiber Reinforced Plastic) Cable Tray Pultrusion Machine. This cutting-edge technology showcases the company's commitment to providing state-of-the-art machinery solutions for the cable management industry. With a focus on enhanced productivity, efficiency, and durability, this new machine is set to revolutionize the sector in numerous ways.Paragraph 1:The FRP Cable Tray Pultrusion Machine is a result of extensive research and development, combined with the company's years of experience in the field. Pultrusion is a continuous manufacturing process that produces fiber-reinforced polymer composites with superior mechanical properties. By utilizing this innovative approach, the machine is designed to create cable trays with exceptional strength, rigidity, and resistance to environmental factors such as corrosion and fire.Paragraph 2:Implementing this advanced equipment brings forth a multitude of benefits for industries relying on cable management systems. Firstly, the FRP Cable Tray Pultrusion Machine guarantees high productivity due to its continuous and automated manufacturing process. This allows for the production of cable trays at a much faster rate compared to conventional methods, resulting in significant time and cost savings.Paragraph 3:Furthermore, the FRP Cable Tray Pultrusion Machine ensures precise and uniform product dimensions. By controlling variables such as resin content, fiber density, and temperature throughout the manufacturing process, the machine delivers cable trays with consistent quality and reliability. This feature eliminates the need for excess materials or rework, leading to further cost reduction and waste minimization.Paragraph 4:One of the most significant advantages of the FRP Cable Tray Pultrusion Machine is its durability and resistance to external influences. Traditional metal cable trays are prone to rust, corrosion, and degradation over time, affecting their performance and longevity. However, the implementation of FRP materials provides excellent resistance to corrosive substances, moisture, UV radiation, and extreme temperatures. This makes the cable trays suitable for both outdoor and indoor applications, including industrial facilities, power plants, transportation infrastructure, and more.Paragraph 5:Moreover, the FRP Cable Tray Pultrusion Machine promotes environmental sustainability by utilizing lightweight, recyclable, and non-toxic materials. The reduction in weight compared to traditional metal cable trays significantly reduces transportation costs and energy consumption during installation. Additionally, the longevity of FRP cable trays minimizes the need for replacements, preventing unnecessary waste generation.Paragraph 6:The company's commitment to customer satisfaction is reflected in the FRP Cable Tray Pultrusion Machine's user-friendly features. With its intuitive control panel and automated operation, the machine ensures ease of use and minimal training requirements for operators. This not only improves overall efficiency but also reduces human errors during the production process, leading to enhanced product quality.Conclusion:In conclusion, the introduction of the FRP Cable Tray Pultrusion Machine marks a significant milestone in the cable management industry. Through its advanced technology, this innovative machinery brings improved productivity, cost-effectiveness, and durability to cable tray manufacturing. With its ability to withstand diverse environmental conditions and promote sustainability, the FRP Cable Tray Pultrusion Machine is set to redefine the standard for cable management systems across various sectors.