High-Quality W-Beam Crash Barrier Machine for Sale - Get Yours Today!
By:Admin
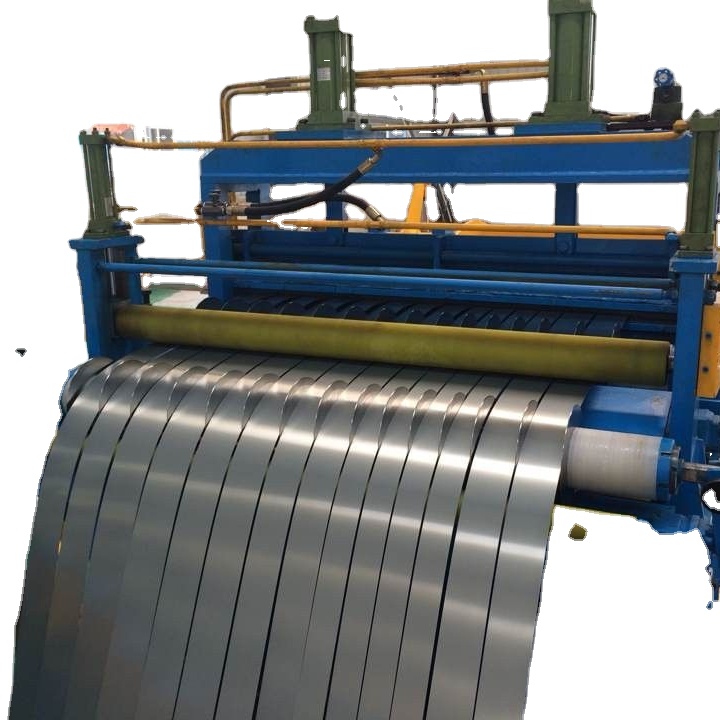
In the world of highway safety, the importance of crash barriers cannot be overstated. These vital structures are designed to prevent vehicles from colliding with obstacles such as trees, buildings, or other vehicles in the event of an accident. As such, the quality and integrity of these barriers are of utmost importance.
Recognizing the critical role that crash barriers play in highway safety, [Company Name] has developed a state-of-the-art W Beam Crash Barrier Machine, which is set to revolutionize the way these crucial structures are manufactured and installed.
[Company Name] has long been a leader in the field of highway safety equipment, with a strong reputation for producing high-quality products that meet the strictest standards of safety and reliability. The company’s commitment to innovation and excellence is evident in its latest offering – the W Beam Crash Barrier Machine.
This cutting-edge machine is designed to streamline the production and installation of W-beam crash barriers, making the process more efficient and cost-effective than ever before. With its advanced technology and precision engineering, the W Beam Crash Barrier Machine is capable of producing barriers of unparalleled quality and durability, ensuring the safety of motorists on highways around the world.
One of the key features of the W Beam Crash Barrier Machine is its versatility. The machine is capable of producing a wide range of barrier designs, making it suitable for use in a variety of highway environments. Whether it’s a straight section of highway, a curved road, or a complex interchange, the W Beam Crash Barrier Machine can be customized to meet the specific needs of any project.
In addition to its versatility, the W Beam Crash Barrier Machine is also incredibly efficient. Its high-speed production capabilities mean that barriers can be manufactured and installed in a fraction of the time it would take using traditional methods, saving time and money for highway authorities and contractors. Furthermore, the machine’s automated processes minimize the risk of human error, ensuring that each barrier meets the highest standards of quality and safety.
Another standout feature of the W Beam Crash Barrier Machine is its durability. Constructed from high-grade materials and built to withstand the rigors of continuous use, the machine is designed to provide years of reliable service, making it a sound investment for any organization involved in highway safety.
The launch of the W Beam Crash Barrier Machine represents a significant step forward in the field of highway safety equipment. With its advanced technology, versatile design, and efficient production capabilities, the machine is set to revolutionize the way crash barriers are manufactured and installed, ultimately enhancing safety on highways around the world.
As [Company Name] continues to lead the way in the development of innovative highway safety solutions, the launch of the W Beam Crash Barrier Machine is a testament to the company’s commitment to excellence and its dedication to keeping motorists safe on the road. With its unparalleled quality and efficiency, this groundbreaking machine is a game-changer for the highway safety industry, and is sure to make a lasting impact on the way crash barriers are produced and installed in the years to come.
Company News & Blog
High-quality Steel Roofing Sheet Roof Tile Forming Machine: A Reliable Solution for 0.6mm 1219mm Sheets
Title: High-Quality Steel Roofing Sheet Roof Tile Forming Machine Now Available in ChinaIntroduction:China has become a global leader in manufacturing machinery and equipment, offering cutting-edge solutions for a wide range of industries. Adding to its repertoire is the introduction of a high-quality 0.6mm 1219mm Steel Roofing Sheet Roof Tile Forming Machine. Produced by a renowned Chinese manufacturer, this machine promises to revolutionize the roofing industry with its superior performance and durability.Advancements in technology have significantly contributed to the development of more efficient roofing solutions. The new 0.6mm 1219mm Steel Roofing Sheet Roof Tile Forming Machine offers exceptional features that ensure the production of top-notch roofing tiles. With strict quality control measures in place, this advanced machinery is proving to be a game-changer in the field of cold roll forming.Product Features:The 0.6mm 1219mm Steel Roofing Sheet Roof Tile Forming Machine boasts an array of impressive features that set it apart from other machines in the market. Let's take a closer look:1. Robust Construction: The machine is manufactured using high-quality materials, ensuring durability and reliability in its performance. Its sturdy frame and components make it a long-lasting asset in any manufacturing setup.2. Precision Engineering: This machine utilizes advanced technology to ensure precision and accuracy in the production of roofing tiles. Every detail is meticulously crafted, resulting in consistent and uniform tiles that meet the highest industry standards.3. Efficient Production: Equipped with a powerful motor, the machine operates at optimal speeds, enabling high-volume production without compromising on quality. Its automated processes reduce manual labor and increase efficiency, minimizing production time and costs.4. Versatility: The machine is designed to work with a wide range of materials, including steel, to produce various types of roofing tiles. This versatility allows manufacturers to cater to different consumer demands, expanding their market reach.5. User-Friendly Interface: The machine's user-friendly interface ensures easy operation, even for those with minimal experience in roll forming. Its intuitive controls and clear instructions make it accessible to a broader range of users, accelerating production and minimizing errors.Company Introduction:The 0.6mm 1219mm Steel Roofing Sheet Roof Tile Forming Machine is manufactured by a prominent Chinese company well-known for its expertise in sheet roll forming machinery. With years of experience and a commitment to excellence, this manufacturer has established itself as a reliable and trusted provider of innovative machinery solutions.The company's state-of-the-art manufacturing facility and skilled workforce enable the production of high-quality machines that meet global standards. Along with the 0.6mm 1219mm Steel Roofing Sheet Roof Tile Forming Machine, they offer a comprehensive range of sheet roll forming machines tailored to various industries.Conclusion:The introduction of the high-quality 0.6mm 1219mm Steel Roofing Sheet Roof Tile Forming Machine from China marks a significant advancement in the roofing industry. With its robust construction, precision engineering, efficient production capabilities, and user-friendly interface, this machine empowers manufacturers to produce superior-quality roofing tiles with ease.As China continues to lead in technological advancements, this latest offering further strengthens its position as a global powerhouse in machinery manufacturing. Manufacturers worldwide can now benefit from this excellent roofing sheet roll forming machine, ensuring increased productivity, improved product quality, and ultimately, enhanced customer satisfaction.
High-Quality W-Beam Crash Barrier Machine for Sale - Get Yours Today!
W Beam Crash Barrier Machine boosts safety on highwaysIn the world of highway safety, the importance of crash barriers cannot be overstated. These vital structures are designed to prevent vehicles from colliding with obstacles such as trees, buildings, or other vehicles in the event of an accident. As such, the quality and integrity of these barriers are of utmost importance.Recognizing the critical role that crash barriers play in highway safety, [Company Name] has developed a state-of-the-art W Beam Crash Barrier Machine, which is set to revolutionize the way these crucial structures are manufactured and installed.[Company Name] has long been a leader in the field of highway safety equipment, with a strong reputation for producing high-quality products that meet the strictest standards of safety and reliability. The company’s commitment to innovation and excellence is evident in its latest offering – the W Beam Crash Barrier Machine.This cutting-edge machine is designed to streamline the production and installation of W-beam crash barriers, making the process more efficient and cost-effective than ever before. With its advanced technology and precision engineering, the W Beam Crash Barrier Machine is capable of producing barriers of unparalleled quality and durability, ensuring the safety of motorists on highways around the world.One of the key features of the W Beam Crash Barrier Machine is its versatility. The machine is capable of producing a wide range of barrier designs, making it suitable for use in a variety of highway environments. Whether it’s a straight section of highway, a curved road, or a complex interchange, the W Beam Crash Barrier Machine can be customized to meet the specific needs of any project.In addition to its versatility, the W Beam Crash Barrier Machine is also incredibly efficient. Its high-speed production capabilities mean that barriers can be manufactured and installed in a fraction of the time it would take using traditional methods, saving time and money for highway authorities and contractors. Furthermore, the machine’s automated processes minimize the risk of human error, ensuring that each barrier meets the highest standards of quality and safety.Another standout feature of the W Beam Crash Barrier Machine is its durability. Constructed from high-grade materials and built to withstand the rigors of continuous use, the machine is designed to provide years of reliable service, making it a sound investment for any organization involved in highway safety.The launch of the W Beam Crash Barrier Machine represents a significant step forward in the field of highway safety equipment. With its advanced technology, versatile design, and efficient production capabilities, the machine is set to revolutionize the way crash barriers are manufactured and installed, ultimately enhancing safety on highways around the world.As [Company Name] continues to lead the way in the development of innovative highway safety solutions, the launch of the W Beam Crash Barrier Machine is a testament to the company’s commitment to excellence and its dedication to keeping motorists safe on the road. With its unparalleled quality and efficiency, this groundbreaking machine is a game-changer for the highway safety industry, and is sure to make a lasting impact on the way crash barriers are produced and installed in the years to come.
High-Quality Aluminium Corrugation Machine for Your Business Needs
Aluminium Corrugation Machine Revolutionizes Manufacturing ProcessThe manufacturing industry is constantly evolving, with new innovations and technologies continuously changing the way products are produced. One such innovation is the Aluminium Corrugation Machine, which has revolutionized the process of shaping and corrugating aluminum sheets.The Aluminium Corrugation Machine, manufactured by an industry-leading company, is a state-of-the-art piece of equipment that has redefined the corrugation process. The machine is designed to increase production efficiency and improve the quality of corrugated aluminum sheets, making it an essential tool for manufacturers in various industries.The Aluminium Corrugation Machine utilizes advanced technology to ensure precise and consistent corrugation of aluminum sheets. This not only improves the overall quality of the final product but also reduces waste and increases productivity. The machine's automated features and user-friendly interface make it easy to operate, allowing for seamless integration into existing manufacturing processes.The company behind the Aluminium Corrugation Machine is a renowned leader in the manufacturing industry, with a long-standing reputation for producing high-quality machinery and equipment. With a focus on innovation and continuous improvement, the company has developed a wide range of cutting-edge products that cater to the diverse needs of manufacturers across various sectors.In addition to the Aluminium Corrugation Machine, the company offers a comprehensive range of solutions for aluminum processing, including roll forming machines, cutting machines, and various other equipment essential for the manufacturing process. With a commitment to delivering superior products and exceptional customer service, the company has established itself as a trusted partner for manufacturers worldwide.The Aluminium Corrugation Machine has already made a significant impact on the manufacturing industry, with many companies adopting this innovative technology to enhance their production capabilities. By incorporating this advanced machine into their operations, manufacturers have been able to streamline their processes, reduce production costs, and ultimately deliver better products to their customers.One of the key advantages of the Aluminium Corrugation Machine is its versatility. The machine is suitable for a wide range of applications, from roofing and cladding to automotive and aerospace components. This flexibility allows manufacturers to expand their product offerings and explore new opportunities in the market, driving growth and innovation within their businesses.Furthermore, the Aluminium Corrugation Machine is designed with sustainability in mind. By improving the efficiency of the corrugation process, the machine helps to minimize material wastage and energy consumption, contributing to a more environmentally friendly manufacturing practice. This aligns with the growing demand for sustainable solutions within the industry and positions the machine as a valuable asset for manufacturers looking to reduce their environmental impact.Looking ahead, the company continues to invest in research and development to further enhance the capabilities of the Aluminium Corrugation Machine. With a focus on continuous improvement and innovation, the company is committed to staying at the forefront of the manufacturing industry and providing cutting-edge solutions that meet the evolving needs of its customers.The Aluminium Corrugation Machine represents a significant leap forward in aluminum processing technology, offering manufacturers a powerful tool to elevate their production capabilities and drive business growth. With its advanced features, precision engineering, and commitment to sustainability, the machine has earned its place as a game-changer in the manufacturing industry, paving the way for a more efficient and sustainable future.
Highly Efficient Slitter with Razor and Rotating Knife Cutting Systems for Flexible and Rigid Materials, 1300mm Width
Title: Slitter - BRASIA LTDA Introduces 1300 mm Wide Automatic Roll Slitter for Versatile Material CuttingSubtitle: Cutting-Edge Technology Enhances Precision and Efficiency in Material Processing[date][City], [Country] – Slitter - BRASIA LTDA, a leading provider of innovative cutting solutions, has recently unveiled its latest offering, an advanced 1300 mm wide Automatic Roll Slitter. With its exceptional razor and rotating knife cutting systems, this versatile machine is capable of handling a wide range of flexible and rigid materials, empowering industries with enhanced productivity and precision.1- Efficient Cutting of Flexible Materials:Equipped with a razor cutting system and special articulated support, the 1300 mm Automatic Roll Slitter is specifically designed to cater to the cutting needs of flexible materials. From BOPP, PP, PE, PVC, to non-printed materials, this cutting-edge machine ensures clean and precise cuts, enhancing the efficiency of production processes.2- Seamless Cutting of Rigid and Semi-Rigid Materials:In addition to its razor cutting system, this innovative slitter also features a rotating knife cutting system. This unique capability enables the machine to effortlessly handle rigid and semi-rigid materials such as card paper, cardboard, stamped paper, felt, and laminated materials, expanding its application across various industries.3- Wide Roll Entry and Smooth Alignment:The 1300 mm Automatic Roll Slitter boasts a spacious roll entry point with a diameter of 1000 mm. This not only allows for easy loading and unloading of materials but also ensures smooth alignment, minimizing downtime during operation. The inclusion of an aligner, air shaft, and electromagnetic control further optimizes the slitting process.4- Enhanced Output and Control:To maximize productivity, the slitter is equipped with double articulated air shafts, ensuring efficient winding of slit materials. With individual electromagnetic control, operators have precise control over the winding process, preventing any potential material damage or inconsistency.5- Accurate Reading with Electric Photo Cell:Incorporating cutting-edge technology, the 1300 mm Automatic Roll Slitter is equipped with an electric photo cell. This feature enables the machine to accurately read lengthwise printing, allowing for precise cutting based on specific patterns or designs.6- Convenient Meter Counter:This sophisticated slitter also features a meter counter with an electronic sensor. This enables operators to track the length of materials being processed, ensuring precise measurements and reducing waste.7- Advanced Automatic Stop Sensor:The Automatic Roll Slitter is designed with an automatic stop sensor, which halts the machine upon completion of the programmed measurement. This ensures optimal efficiency and prevents any potential material waste.8- Speed Control at Your Fingertips:To cater to diverse processing needs, this state-of-the-art slitter offers speed control through digital programming. Operators can easily adjust the cutting speed to meet the requirements of different materials, providing versatility and convenience.9- User-Friendly Digital Control Panel:All operational functions of the 1300 mm Automatic Roll Slitter are effortlessly programmed using a digital control panel. With programmed memory functions, users can conveniently store and recall specific settings, streamlining the overall production process.Slitter - BRASIA LTDA's new 1300 mm Automatic Roll Slitter represents a significant advancement in material cutting technology. Its superior cutting systems, precise controls, and user-friendly features make it an unrivaled choice for industries seeking to enhance productivity, streamline processes, and achieve impeccable cutting results.For more information on the 1300 mm Automatic Roll Slitter and its wide range of applications, please contact:[Contact Information]About Slitter - BRASIA LTDA:Slitter - BRASIA LTDA specializes in the development and production of advanced cutting solutions. With a commitment to innovation, reliability, and customer satisfaction, the company has established itself as a trusted provider of cutting-edge technologies in the industry.
European Standard C Z Purlin Machine with Interchangeable Punching Hole Features
In recent years, the construction industry has undergone a significant transformation. New technologies and innovative solutions have made construction projects more efficient, faster, and, most importantly, safer. One such technology is the C Z Purlin Punching Holes Interchangeable Making Machine (CZPM), which has become extremely popular in Europe.This machine is designed to manufacture C and Z-shaped steel channels that are commonly used in building construction. The CZPM is an automated system that can produce C and Z-shaped purlins of varying sizes and lengths, with pre-punched holes that are interchangeable. This system is not only cost-effective and time-saving but also guarantees precision and accuracy.In the past, purlins were produced using traditional methods that were slow, laborious, and often inaccurate. However, with the advent of the CZPM, purlin production has become smoother and more efficient. The machine can produce purlins with widths ranging from 80mm to 300mm, and heights ranging from 30mm to 100mm, making it possible to cater to a wide range of construction needs.The CZPM is equipped with a punching unit that allows for the creation of holes of varying shapes and sizes, according to the requirements of the construction project. This means that purlins can be produced with holes for wiring, plumbing, and other services, without the need for additional drilling or cutting.Another notable feature of the CZPM is its versatility. The machine can produce purlins made of various materials, including galvanized steel, hot-rolled steel, and aluminum. This flexibility makes it an ideal solution for both small and large-scale construction projects.Furthermore, the CZPM is designed to be user-friendly, with an intuitive interface and easy-to-use controls. The machine requires minimal operator training, and the automated system ensures that the purlins produced are of consistent quality.Many construction companies across Europe have already embraced the CZPM, recognizing its numerous benefits and potential impact on the industry. This technology has revolutionized the way purlins are produced and has made construction projects faster, more accurate, and more cost-effective.One company that has adopted this technology is {company name}, a leading manufacturer of steel building products in Europe. Founded in 2002, the company has been at the forefront of innovative steel solutions, serving a wide range of clients in the construction industry.As a company committed to delivering quality steel products, {company name} recognizes the importance of investing in advanced technologies such as the CZPM. With this machine, the company can produce high-quality purlins that meet the specific needs of each client.In addition, {company name} is known for its commitment to sustainability and environmentally-friendly practices. The CZPM aligns with this core value as it minimizes waste and reduces the carbon footprint associated with purlin production.Over the years, {company name} has established itself as a trusted partner for construction companies across Europe, delivering reliable and high-quality products. As the construction industry continues to evolve, {company name} is committed to remaining at the forefront of innovation and providing innovative steel solutions for its clients.In conclusion, the CZPM is a game-changer for the construction industry, making purlin production faster, more efficient, and more precise. Companies like {company name} are embracing this technology and leveraging its benefits to meet the evolving needs of their clients. As the construction industry continues to grow and evolve, the CZPM will undoubtedly play a vital role in shaping its future.
Revolutionary rollformer technology advances construction industry
The latest addition to the metal construction industry, an advanced rollformer, is set to revolutionize the way buildings are constructed. This cutting-edge technology, developed by a renowned company, promises to streamline the construction process and deliver superior quality structures in a cost-effective manner.The rollformer, developed by a highly reputable company, takes metal construction to new heights. Its precise engineering and innovative design ensure that buildings are constructed efficiently and with utmost precision. This advanced technology allows for rapid assembly of metal frames, significantly reducing construction time and costs.The rollformer employs state-of-the-art automation features, enabling seamless integration with CAD (Computer-Aided Design) software. The synergy between the rollformer and the company's advanced software allows for precise customization of metal frames, catering to the unique requirements of each project. With the ability to automatically generate accurate measurements and specifications, the rollformer eliminates human error and ensures seamless integration of structural elements.In addition to its superior automation capabilities, the rollformer boasts a durable and robust construction. With high-quality materials used in its manufacturing, the rollformer guarantees a long lifespan, ensuring uninterrupted operation for years to come. Its reliability and consistency make it the preferred choice for large-scale construction projects, where precision and speed are of the essence.The rollformer offers numerous advantages over traditional construction methods. Its ability to fabricate metal frames on-site eliminates the need for transporting pre-fabricated components, reducing transport costs and logistical complexities. Moreover, the rollformer eliminates the need for complex on-site welding, thereby enhancing the safety of the construction process.One of the key features of this rollformer is its adaptability to various types of metal. Whether it's steel, aluminum, or other metal alloys, the rollformer can efficiently fabricate frames using the material of choice for each project. This versatility expands the possibilities for architects and construction companies, enabling them to explore innovative designs without compromising on quality or functionality.The rollformer's impact on the construction industry is not limited to efficiency and quality. Its environmentally friendly design aligns with the global push for sustainable construction practices. By minimizing waste generation and optimizing resource utilization, the rollformer significantly reduces the carbon footprint associated with traditional construction methods. This environmentally conscious approach makes it an ideal choice for companies aiming to contribute towards a greener future.Furthermore, the rollformer's realization of rapid assembly of metal frames opens up opportunities for companies to take on larger projects. The increase in efficiency and cost-effectiveness provided by the rollformer allows construction companies to not only complete projects faster but also take on more contracts simultaneously. This leads to economic growth within the industry by creating more job opportunities and stimulating overall development.With its revolutionary rollformer, this innovative company is set to disrupt the metal construction industry. By combining cutting-edge automation with superior quality materials, the rollformer streamlines the construction process while delivering impeccable structures. Its adaptability, durability, and environmental consciousness make it the go-to choice for construction companies seeking to enhance their operations and contribute towards a sustainable future.In conclusion, the introduction of the rollformer signifies a remarkable advancement in the metal construction industry. The combination of advanced automation, precise engineering, and adaptability to various metals positions it as a game-changer. As construction companies strive to meet increasing demands for efficiency, quality, and sustainability, the rollformer emerges as the perfect solution to stay ahead of the curve.
Efficient 16 Gauge Sheet Metal Slitter: All You Need to Know
{Insert Company Name}, a leading manufacturer of industrial machinery, is proud to announce the release of its latest innovation, the 16 Gauge Sheet Metal Slitter. This state-of-the-art machine is designed to revolutionize the metal slitting industry, providing customers with unprecedented levels of efficiency and precision.Sheet metal slitting is a crucial process in various industries, including construction, automotive, and manufacturing, where sheets of metal are cut into smaller, more manageable strips. Traditionally, this task has been approached using cumbersome and time-consuming techniques. However, with the introduction of the 16 Gauge Sheet Metal Slitter by {Insert Company Name}, the process has been streamlined and made considerably more efficient.The 16 Gauge Sheet Metal Slitter stands out from the competition due to its exceptional design and advanced features. Made from high-quality materials, this machine offers unparalleled durability, ensuring a long-lasting and reliable solution for businesses. Its precision-engineered components guarantee consistent and accurate cuts, eliminating the risk of errors or irregularities.One of the key highlights of the 16 Gauge Sheet Metal Slitter is its user-friendly interface. Equipped with an intuitive control panel, operators can easily navigate through the various settings and parameters. Additionally, the machine boasts an ergonomic design, prioritizing the comfort and safety of the users. With adjustable settings and quick changeover capabilities, operators can effortlessly switch between different sheet sizes and materials, enhancing overall productivity.Safety is a top priority at {Insert Company Name}, and the 16 Gauge Sheet Metal Slitter reflects this commitment. The machine is equipped with comprehensive safety features, including emergency stop buttons, safety guards, and intelligent sensors that detect any anomalies or potential hazards. This ensures maximum protection for operators and minimizes the risk of accidents or injuries in the workplace.Another key feature of the 16 Gauge Sheet Metal Slitter is its versatility. This machine is capable of handling a wide range of sheet metal materials, including stainless steel, aluminum, and galvanized steel. With adjustable cutting speeds and precision-guided blades, it can easily accommodate different thicknesses and widths of metal, making it suitable for various applications.With the 16 Gauge Sheet Metal Slitter, {Insert Company Name} aims to provide customers with a solution that not only improves efficiency but also saves time and reduces costs. By automating the slitting process, businesses can significantly increase their production output while maintaining consistent quality. This, in turn, leads to higher profitability and a competitive edge in the market.In addition to its exceptional performance, {Insert Company Name} also prides itself on providing excellent customer support. Their team of experienced technicians is available to assist customers with installation, training, and ongoing maintenance, ensuring a smooth and hassle-free experience throughout the lifespan of the machine.As the metal industry continues to evolve and demand for efficient slitting solutions increases, {Insert Company Name} remains at the forefront of innovation. With the introduction of the 16 Gauge Sheet Metal Slitter, they continue to push boundaries and offer cutting-edge solutions to meet the diverse needs of their customers.In conclusion, the 16 Gauge Sheet Metal Slitter by {Insert Company Name} is set to redefine the metal slitting industry. With its advanced features, user-friendly interface, and unmatched versatility, this machine is poised to become an indispensable tool for businesses seeking to improve their productivity and competitiveness. {Insert Company Name} yet again raises the bar with this innovative solution, solidifying its reputation as a leader in the field of industrial machinery.
How to Build a Sheet Metal Barn in 6 Easy Steps: A Step-by-Step Guide
article.If you’re looking for a sturdy and durable structure to protect your property or livestock from the elements, then building a sheet metal barn may be the solution for you. Sheet metal barns are a cost-effective and easy-to-build option that offers a long-lasting shelter for your animals, equipment, and machinery. In this article, we provide you with six easy steps to build your own sheet metal barn.Step 1: Plan Your BarnThe first step in building your sheet metal barn is to gather all the necessary information. This includes determining the size of the barn you need, choosing the right location, getting appropriate permits and approvals, and creating a detailed plan. A full-scale model and an accurate blueprint will help you to visualize the structure, avoid costly errors, and ensure that your barn meets local building codes and regulations.Step 2: Pour Your FoundationWith your plan in hand, the next step is to pour a solid foundation for your sheet metal barn. Concrete is the most common material used for this purpose, but you can also use wood posts or piers. The foundation must be durable and strong enough to support the weight of the structure and withstand harsh weather conditions.Step 3: Erect Your FrameOnce the foundation is in place and has had time to cure, the next step is to erect the frame of your sheet metal barn. Wood or steel posts are the most popular materials for frames, but you can also use other materials, such as concrete. The frame should be level and square to ensure that the sheet metal panels fit perfectly and the barn is structurally sound.Step 4: Install Your Roof and WallsWith the frame completed, the next step is to install the roof and walls of your sheet metal barn. Galvanized sheet metal is a popular option due to its durability, strength, and resistance to rust and corrosion. You can also use other materials, such as polycarbonate panels, to add natural light and ventilation. Sheet metal panels should be installed securely, with appropriate screws and anchors, to prevent water leakage and damage.Step 5: Add Your Doors and WindowsTo complete your sheet metal barn, add doors and windows as needed. Large doors for machinery and smaller doors for livestock are essential, and windows can provide natural light and ventilation. Make sure that doors and windows are appropriately secured and protected from the elements to ensure the safety of your animals and equipment.Step 6: Finishing TouchesFinally, add any finishing touches, such as insulation, ventilation, and gutters, to your sheet metal barn. These features will help to improve the comfort and safety of your animals and equipment, and protect your barn from water damage.ConclusionBuilding a sheet metal barn may seem daunting, but by following these six easy steps, you can create a durable and functional structure that meets your needs and budget. With careful planning, appropriate materials, and attention to detail, your sheet metal barn will provide you with years of protection and peace of mind.
Efficient Roll Forming Machine for Light Gauge Steel Keel Production
Title: Revolutionary Light Gauge Steel Keel Roll Forming Machine Revolutionizes Construction IndustryIntroduction: [Company Name], an industry-leading manufacturer of construction machinery, has recently unveiled its latest innovation, a groundbreaking Light Gauge Steel Keel Roll Forming Machine. This state-of-the-art machine is set to revolutionize the construction industry by significantly increasing efficiency and reducing labor costs in the production of light gauge steel frames and structures. With its unique features and advanced technology, the Light Gauge Steel Keel Roll Forming Machine is poised to become an indispensable tool for modern construction projects.Paragraph 1: Traditional methods of constructing light gauge steel structures can be labor-intensive and time-consuming. However, the Light Gauge Steel Keel Roll Forming Machine eliminates these barriers by automating the process with precision and speed. This advanced technology enables the production of consistent and high-quality steel frames, significantly reducing waste material and time spent on manual labor.Paragraph 2: The Light Gauge Steel Keel Roll Forming Machine operates on the principles of roll forming, which involves feeding a coil of flat steel through a series of rollers, gradually shaping it into the desired cross-sectional profile. With precise control and selection of raw materials, this machine provides highly accurate and uniform results, ensuring the structural integrity of the final products.Paragraph 3: The Light Gauge Steel Keel Roll Forming Machine boasts an array of features that set it apart from traditional methods. Its automated nature allows for continuous production without the need for manual intervention. Additionally, its modular design and customizable options cater to various project requirements, offering flexibility and adaptability.Paragraph 4: The Light Gauge Steel Keel Roll Forming Machine incorporates cutting-edge technology, including computer numerical control (CNC) systems. This automation ensures precise measurements and consistent panel lengths, minimizing errors. The machine's user-friendly interface enables easy operation and adjustment of parameters, making it accessible to both experienced professionals and newcomers to the industry.Paragraph 5: [Company Name] has invested significant resources into research and development to create a machine that not only enhances productivity but also prioritizes safety. The Light Gauge Steel Keel Roll Forming Machine is equipped with safety features, such as emergency stop buttons and protective barriers, ensuring a secure working environment for operators.Paragraph 6: The introduction of the Light Gauge Steel Keel Roll Forming Machine is expected to have far-reaching implications for the construction industry. Its efficiency and affordability make it an attractive option for large-scale projects, such as residential buildings, commercial complexes, and industrial facilities. The reduced labor costs associated with this machine represent a significant advantage in today's competitive construction market.Paragraph 7: The Light Gauge Steel Keel Roll Forming Machine aligns with global sustainability goals, as it promotes the use of lightweight steel structures that offer energy efficiency, durability, and recyclability. By minimizing waste and optimizing material utilization, this machine supports environmentally friendly construction practices.Conclusion: With its groundbreaking technology, the Light Gauge Steel Keel Roll Forming Machine is set to redefine the construction industry. By streamlining the production process, increasing precision, and reducing labor costs, this cutting-edge machine will undoubtedly play a crucial role in the development of sustainable and efficient structures worldwide. [Company Name]'s commitment to innovation has once again propelled the industry forward, offering a transformative solution for the construction sector.
New roll former for producing drip edge now available
Automated roll forming technology has been making waves in the construction industry, as it significantly improves the efficiency and accuracy of producing various components used in building structures. One such company at the forefront of advancing this technology is {Company Name}, a leading manufacturer of roll forming machines and components.{Company Name} has recently introduced a cutting-edge Drip Edge Roll Former that is set to revolutionize the production of drip edges for roofing systems. This state-of-the-art machine is designed to create custom drip edges with precision and speed, enabling contractors and building professionals to enhance the quality and durability of their roofing installations.The Drip Edge Roll Former utilizes advanced roll forming techniques to transform metal coils into seamless drip edges that provide essential protection against water damage and improve the overall integrity of the roof. With its computer-controlled automation, the machine can produce drip edges of varying sizes and configurations, tailored to fit the specific requirements of different roofing projects.One of the key features of the Drip Edge Roll Former is its ability to handle a wide range of metal materials, including galvanized steel, aluminum, and copper, allowing for versatility in design and durability. This flexibility makes it an ideal solution for contractors and builders working on diverse roofing applications, from residential to commercial and industrial projects.Another advantage of the Drip Edge Roll Former is its high-speed production capabilities, which enable efficient manufacturing of drip edges without compromising on quality. The machine's precision and consistency in forming the metal profiles ensure that each drip edge meets the strictest industry standards and specifications.Furthermore, the Drip Edge Roll Former is designed with user-friendly controls and easy changeover features, reducing downtime and enhancing productivity in the production process. Its intuitive interface and quick setup make it accessible to operators of varying skill levels, making it a valuable asset for construction companies looking to streamline their operations.In addition to its technical capabilities, {Company Name} underscores its commitment to providing exceptional support and service to its customers, ensuring that they receive the necessary training and assistance to maximize the benefits of the Drip Edge Roll Former. The company's team of experts is dedicated to helping clients integrate the machine seamlessly into their production workflows and achieve optimal results.The launch of the Drip Edge Roll Former reflects {Company Name}'s continuous innovation and dedication to advancing roll forming technology to meet the evolving needs of the construction industry. With its focus on precision, efficiency, and reliability, the machine is positioned to become a game-changer in the production of drip edges, offering a competitive edge to businesses seeking to elevate their roofing solutions.As the demand for high-quality roofing components continues to grow, {Company Name} remains at the forefront of delivering cutting-edge roll forming solutions that empower construction professionals to achieve superior results in their projects. The Drip Edge Roll Former stands as a testament to the company's commitment to excellence and its unwavering pursuit of innovation in the field of roll forming technology.In conclusion, with the introduction of the advanced Drip Edge Roll Former, {Company Name} reinforces its position as a leader in the roll forming industry and a trusted partner for businesses seeking to elevate their manufacturing capabilities. The machine's precision, versatility, and efficiency are poised to make a significant impact on the production of drip edges, setting a new standard for quality and performance in roofing systems.